Mining Thickener operation manual pdf: Beginners guide
2022-10-18
staurk machinery
1. Overview
Technical parameter:
Model: NGY45L
Diameter φ45m
Capacity Q=1400m3/h
Peripheral drive center harrow
H=800mm Peripheral linear speed v=8.47m/in
Weekly running time t = 17 minutes 38 seconds
Motor Model: Y112M-4 Power N=4KW Speed: 1500r/min
Application: Mining Thickener is mainly used for the treatment of flotation tailings. The tailings in the tailings are collected, dehydrated and recycled, and the circulating water is reused. The concentration tank is an important place.
Download : Mining Thickener operation manual pdf
Download : Mining Thickener operation manual pdf
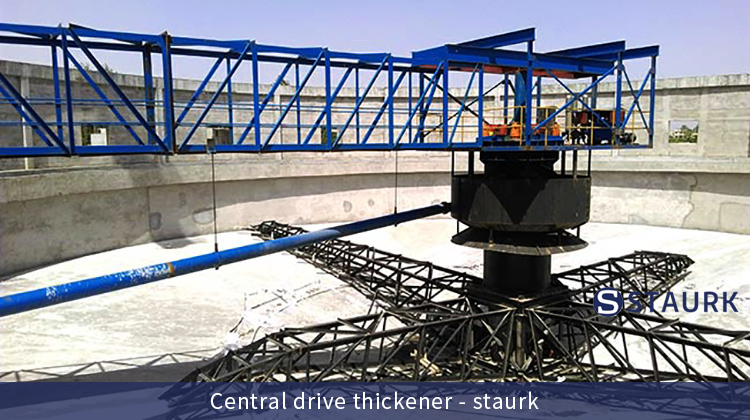
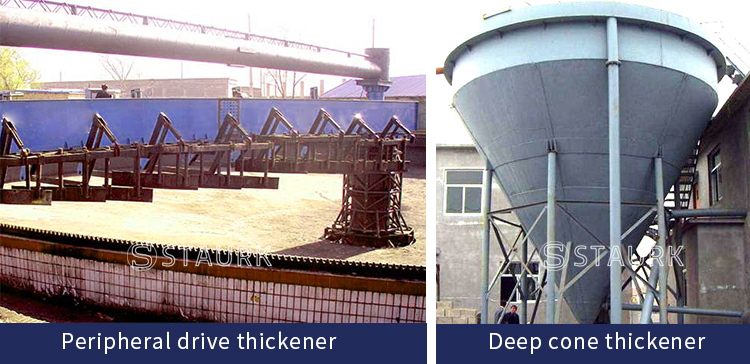
2. General Provisions
1. Drivers must undergo training, pass the examination, and take up the job with the certificate after obtaining the qualification certificate.
2. The driver should master the general structure, working principle, technical characteristics, power supply system and control loop of the thickener.
3. Drivers must strictly implement the shift system and post responsibility system.
4. Fill in all kinds of records carefully as required.
5. Do a good job in the sanitation of equipment and surrounding environment.
6. Wear labor protection supplies (including work clothes, caps, shoes, gloves, earplugs, masks, etc.) as required. Female workers should be placed in their caps. It is forbidden to wear scarves, high heels and slippers or work barefoot on site.
3. Preparations
3.1. Check before driving
① Before driving, you should know the following:
●Learn about the amount of coal washing and the usage of washing water in the last shift.
●Learn about the concentration effect of the previous shift (circulating water, underflow concentration) and the operation of the concentration equipment.
●Learn about the use and addition of flocculants in the last shift, and observe the overflow condition of the concentration tank.
② The surrounding driving track is smooth and free of debris, the double drive motor, reducer, and rollers are well coordinated, and the safety pin is not broken.
③ The overflow weir is flat, and the water tank is smooth without coal sludge accumulation.
④ The center cylinder is well matched with the fixed wheel and the hanging wheel, and there is no wear.
⑤ The hydraulic station should be in good condition, and the manual and automatic raking devices should work sensitively and accurately.
⑥ The central slip ring is well sealed, and no coal slime water splashes into it.
⑦ Handle equipment abnormalities and defects in a timely manner and confirm that they are correct before operating.
3.2. Operator station
After receiving the start signal, the operator enters the enrichment tank, and travels along the beam to the top of the center cylinder to operate and stop. The lifting and lowering of the thickener are carried out automatically. Operators should pay attention to safety when walking on the concentration tank.
4. Equipment operation
4.1 Device startup
After receiving the need to drive information, complete the preparatory work before operation, turn on the power, the indicator light is on, and choose one of the following two methods to start the thickener.
●The automatic/manual selection button is placed in the automatic position to perform automatic operation, and the cycle start button is pressed to automatically lift and drop the rake, and the walking trolley starts automatically after a delay.
●The automatic/manual selection button is pressed to the manual position, and the manual operation is performed. Press the manual button respectively to carry out the lifting and lowering of the rake, the starting and stopping of the walking trolley and the operation of the hydraulic pump.
4.2 Inspection during equipment operation
① According to the feeding situation (concentration, flow rate) overflow and underflow concentration, it is appropriate to add flocculation liquid (concentration between 0.1~0.15%) to ensure the concentration of washing water and meet the coal washing production.
② Pay attention to checking the particle size composition of the underflow, and if it is found that it runs thick, contact the production scheduling in time, check and analyze the reasons, and actively take measures to solve it.
③ Understand the amount of coal slime in the machine (underflow concentration, the load of the thickener), cooperate with the filter press production, discharge underflow evenly, and conduct underflow water circulation in a timely manner if necessary.
④ Whether the temperature rise and sound of the drive motor and reducer are normal, and the insurance pin is in good condition.
⑤ Whether the rollers run smoothly on the track and whether there is any slippage (pay attention to anti-skid in rainy and snowy days, generally dry sand can be sprinkled on the track surface).
⑥ Whether the meshing between the fixed wheel and the hanging wheel and the center cylinder is good, and whether there is any deviation or jamming.
⑦ Whether the hydraulic system is in good working condition, whether each valve body is working normally, and whether the oil pressure indication is normal.
4.3 Equipment shutdown
4.3.1 normal parking
1. After receiving the parking information, the thickener can be stopped automatically or manually, and finally the power supply can be cut off.
2. Due to the hysteresis of the concentration operation, the start, operation and stop of the thickener cooperate with the production of the filter press to meet the underflow concentration standard and ensure that the rake is not pressed after stopping.
4.3.2 emergency pull over
If the following accidents occur during enrichment operation, emergency shutdown should be made:
A. If the coal slurry water splashes into the central slip ring and gets damp and causes a short circuit, it should be reported to the dispatch immediately, and it is required to cut off the power supply and stop the operation.
B. Pay close attention to the change of the load indicator and the status of lifting and dropping the rake. If the rake is found to be jumping, lifting and scraping and other abnormal phenomena, timely notify the dispatcher to take decisive measures to prevent the rake from being pressed and stuck.
C. If the sundries accidentally fall into the machine, the concentration will be too high, causing accidents such as pipe blockage and valve jamming. It should be stopped immediately. (It is strictly forbidden to stack objects and tools on the bridge and the machine table of the thickener)
D. The track is covered with snow and ice, and the rollers of the trolley are slipping. Clean up the snow in time and lay anti-skid materials.
5. Inspection after equipment shutdown
5.1. Check that the gates should be flexible and easy to use, and should be in the switch state of parking; the chute pipeline should be unblocked, and the mechanical and electrical equipment should be in good condition.
5.2. The surrounding driving track is smooth and free of debris, the double drive motor, reducer, and rollers cooperate well, and the safety pin is not broken.
5.3. The overflow weir is flat, and the water tank is smooth without coal sludge accumulation.
5.4. The center cylinder is well matched with the fixed wheel and the hanging wheel, and there is no wear.
5.5. The hydraulic station should be in good condition, and the manual and automatic raking devices should work sensitively and accurately.
6. Equipment maintenance
The mud scraper should be maintained and maintained frequently, and it should be overhauled once a year. During maintenance, it should be done:
1. Replace or add lubricating oil or grease.
2. Check the tightness of the drive device seal.
3. Check the working condition of the hydraulic station and replace the hydraulic oil regularly.
4. Always check whether there is abnormal noise in the transmission parts, whether there is jamming and local wear and so on of each transmission part.
5. After a week of operation for the first time, re-tighten the fasteners and apply butter, and then redo it at regular intervals.
6. It is strictly forbidden to use manpower to push the rotary part of the mud scraper.
7.Operation precautions:
1. It is strictly forbidden to touch the rotating parts of the equipment in operation, and it is strictly forbidden to operate the electrical equipment without authorization; it is strictly forbidden to touch the various buttons with wet fingers; it is strictly forbidden to scrub the electrical equipment with electricity.
2. When the driver walks on the bridge with the thickener, it is strictly forbidden to stick out of the guardrail.
3. The screws of each part of the thickener must be firm and safe. If the pins are interrupted in operation, they should be stopped immediately for repair.
4. The thickener pedestrian walkway must be equipped with railings, and the floor should be made of patterned steel plates and installed firmly.
5. It is strictly forbidden for non-maintenance personnel to check the fixed wheel and hanging wheel on the center cylinder.
6. It is strictly forbidden to store items on the bridge of the thickener to prevent tools and sundries from falling into the pool.
7. The surrounding track of the thickener must be kept flat, smooth and free of obstacles. It is strictly forbidden for anyone to sit or work on the track.
8. The enrichment pool is a safe and important place, and it is strictly forbidden for casual personnel to enter, and there are obvious signs at the entrance.
9. The main hazard factors in this position: ①Coal dust inhalation ②Noise hazard ③Human injury caused by rotating parts ④Equipment defect ⑤Safety protection device defect.
8. Handover
1. Do a good job in the civilized and hygienic work of this post.
2. Explain to the successor clearly the operation of the equipment on duty, the remaining problems and matters needing attention.
3. Assist the on-site inspection of the successor.
4. The problems found shall be handled by the shift personnel, and they shall be reported to the relevant leaders in time when they cannot be handled.
5. Go off work after completing the shift handover procedures as required.
Thickener operating procedures
1. Check before starting
1. When the rake frame is overhauled and debugged when empty, first check that there is no foreign matter jamming between the rake frames; check that the center cylinder is well matched with the fixed wheel and the hanging wheel, and there is no wear.
2. Check that the surrounding driving track is smooth and free of debris, the dual drive motor, reducer, and rollers are well coordinated, the safety pin is not broken, and the reducer is lubricated normally.
3. The hydraulic station should be in good condition, and the manual raking device should work sensitively and accurately. The oil level of the oil tank of the hydraulic station is within the normal scale range.
4. Check whether the control cabinet is powered, and each knob switch is flexible.
2. Start
1. Raise the rake
1.1 Turn the unloading switch to the "unloading" position.
1.2 Press the "hydraulic switch" to start the oil pump of the hydraulic station.
1.3 After the oil pump works normally, turn the "lift switch" to the "lift" position, and at the same time turn the "unload switch" to the "stop" position, observe the pressure display value of the pressure gauge of the hydraulic station, the pressure value is between 5~ 8MPa; at the same time, observe the lifting height of the central barrel (rake), and control the lifting height according to the actual demand.
1.4 After the lifting height of the center barrel (rake frame) meets the actual production requirements, turn the rake lifting switch to the "stop" position, and at the same time turn the "unloading switch" to the unloading position.
1.5 According to the actual needs, if the rake needs to be dropped, the oil pump should not be stopped; if the drop rake operation is not required, turn the "hydraulic switch" to the "stop" position to stop the oil pump.
2. Falling rake
2.1 Turn the unloading switch to the "unloading" position.
2.2 Press the "hydraulic switch" to start the oil pump of the hydraulic station.
1.3 After the oil pump is working normally, turn the "drop rake switch" to the "drop rake" position, and at the same time turn the "unload switch" to the "stop" position, observe the pressure display value of the pressure gauge of the hydraulic station, the pressure value is 5~ 8MPa; at the same time, observe the lifting height of the central barrel (rake), and control the lifting height according to the actual demand.
1.4 After the lifting height of the center barrel (rake frame) meets the actual production requirements, turn the rake lifting switch to the "stop" position, and at the same time turn the "unloading switch" to the unloading position.
1.5 According to the actual needs, if the rake needs to be dropped, the oil pump should not be stopped; if the drop rake operation is not required, turn the "hydraulic switch" to the "stop" position to stop the oil pump. ffffff