China Simmons cone crusher manufacturer Simmons cone crusher manual
2024-07-09
staurk
What is a simmons cone crusher
Simmons cone crusher is an improved, optimized, and updated substitute product for the PY series spring cone crusher. It is a cone crusher designed and developed based on the principle of laminated crushing and the concept of more breaking and less grinding, which integrates high swing frequency, optimized cavity shape, and reasonable stroke. It is suitable for crushing various ores and rocks with medium and above hardness.

Simmons cone crusher parameter
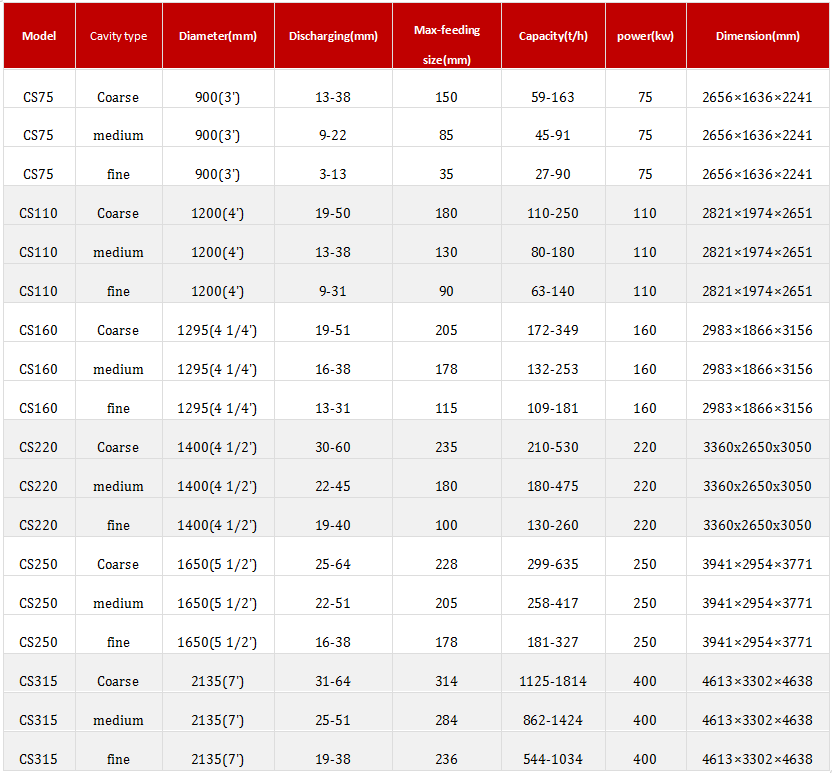
What is the simmons cone crusher structure
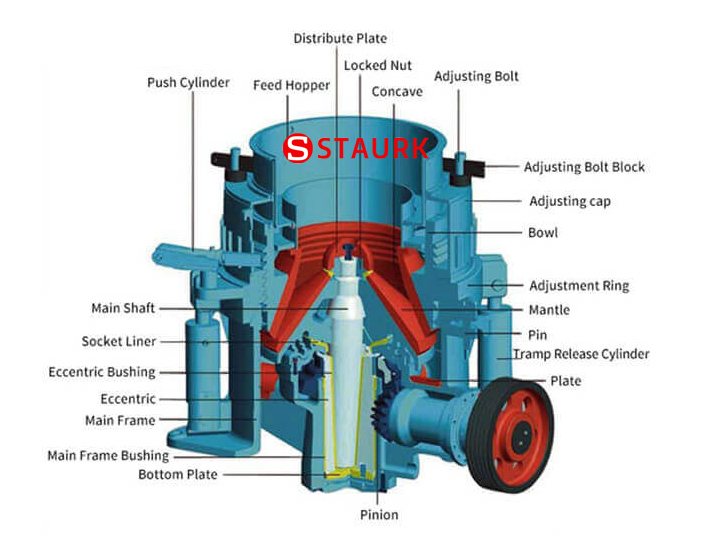
It mainly consists of a frame, a fixed cone assembly, a moving cone assembly, a spring mechanism, a bowl shaped shaft frame, and transmission parts. The auxiliary part consists of an electrical system, a thin oil lubrication system, and a hydraulic cleaning system. High degree of automation and more reliable operations.
Simmons cone crusher Application:
Suitable for non-ferrous metal ores, granite, limestone, quartzite, sandstone, pebbles, iron ore, gold ore, basalt, diabase, and other hard, medium hard ores and rocks.
Application areas of Simmons cone crusher:
Applied in fields such as cement plants, construction, sand and gravel, metallurgy, building materials, road construction, chemical industry, and silicate industry.
How does a simmons cone crusher works, working principle
During the operation of Simmons cone breaking, the eccentric sleeve is driven to rotate by an electric motor through a triangular belt, a large pulley, a transmission shaft, a small bevel gear, and a large bevel gear.
The axis of the broken cone rotates and swings under the drive of the eccentric sleeve, causing the surface of the broken wall to sometimes approach and sometimes leave the surface of the rolling mortar wall.
As a result, the material is continuously impacted, squeezed, and bent in the annular crushing chamber composed of a fixed cone and a moving cone, causing it to break.
The axis of the broken cone rotates and swings under the drive of the eccentric sleeve, causing the surface of the broken wall to sometimes approach and sometimes leave the surface of the rolling mortar wall.
As a result, the material is continuously impacted, squeezed, and bent in the annular crushing chamber composed of a fixed cone and a moving cone, causing it to break.
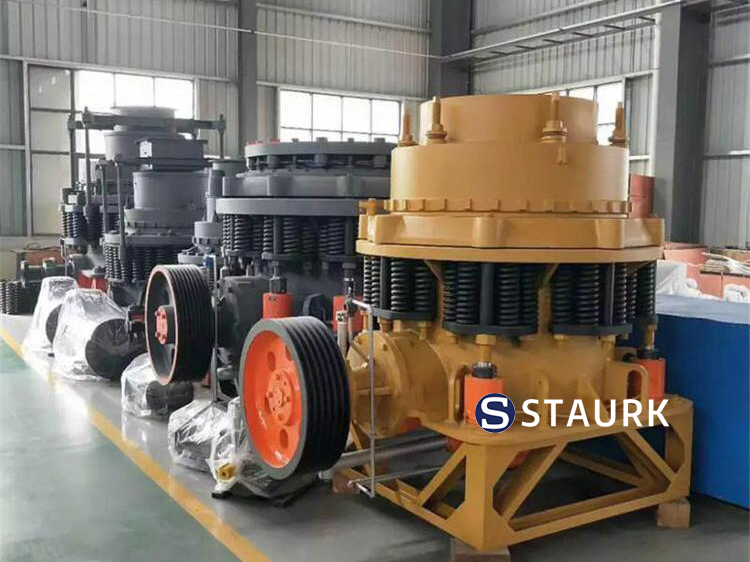
Performance characteristics of Simmons cone crusher
1. Easy to operate and highly automated, it can reduce the particle size of ore entering the mill, achieve more crushing and less grinding, improve the production capacity of the mill, save energy and reduce consumption, and improve the economic benefits of the sand and gravel plant.
2. The connection between the support sleeve and the frame is tightly pressed by a spring. When an unbreakable object such as a metal block falls into the crusher, the spring undergoes compression deformation, expelling foreign objects, achieving safety and preventing machine damage.
3. When an unbreakable foreign object passes through the crushing chamber or the machine is overloaded for some reason, the spring safety system of the cone crusher realizes safety, and the discharge port of the cone crusher increases.
4. Foreign objects are discharged from the crushing chamber of the cone crusher. If foreign objects get stuck in the ore discharge, a cleaning system can be used to increase the ore discharge and allow the foreign objects to be discharged from the crushing chamber of the cone crusher.
5. Under the action of the spring, the cone crusher automatically resets the ore discharge port, and the cone crusher machine returns to normal operation. The surface of the crushing chamber is covered with wear-resistant high manganese steel lining plates. The size of the ore discharge port is adjusted by hydraulic or manual means.
Simmons cone crusher manual
01 The oil temperature is too high.
Cause: Poor oil quality or insufficient oil quantity; Bearing damage; The ambient temperature is too high, there is no cooling water or the cooling water pressure is low; The cooler is blocked.
Solution: Change oil or add oil; Replace bearings; Supply cooling water or increase cooling water pressure; Clean the cooler.
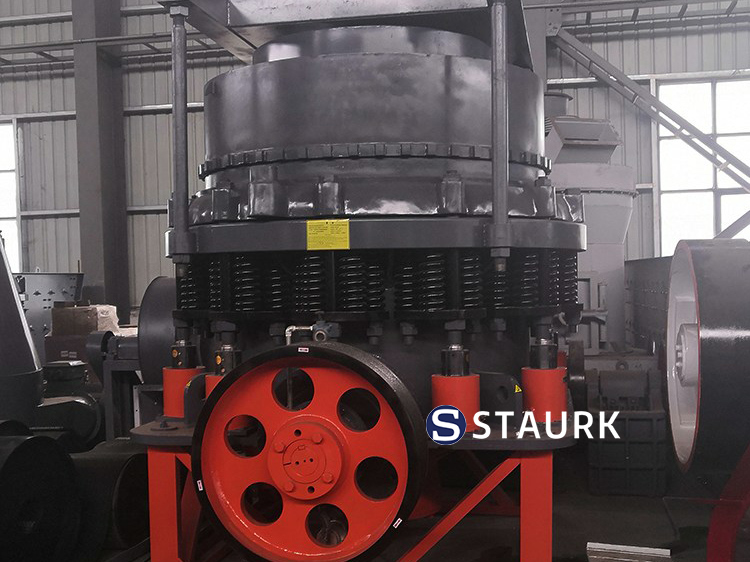
02 Oil temperature and oil pressure rise.
Cause: Oil pipe or oil ditch blockage, safety valve failure.
Solution: Stop the machine for inspection and repair.
03 After the oil pump starts, the oil pressure is low or the indicator shows no oil flow.
Cause: Low oil temperature; Oil pipe blockage or abnormal oil pump operation.
Solution: Heat up to increase oil temperature; Repair the pipeline or oil pump.
04 oil contains a large amount of fine mud and impurities.
Cause: Sealing and dust prevention device malfunction; Blockage or leakage of water pipes causing water shortage.
Solution: Stop the machine, reseal or clean for maintenance, and replace with new oil.
05There is water in the 05 oil, and the oil level in the tank rises.
Cause: Water enters the thin oil station; The cooler is leaking and the water pressure is greater than the oil pressure; Small cone breakage with excessive water supply or clogged return pipe.
Solution: Cover the thin oil station with a canopy, clean the fuel tank, and replace the engine oil; Repair the leaking part or replace the cooler, reduce water pressure, clean the oil tank, and replace the engine oil; Adjust the water supply or clean the return pipe, clean the oil tank, and replace with new oil.
06 crusher vibrates strongly.
Cause: The fixing device of the machine base is loose; The crushing chamber enters the difficult to crush material; Excessive material in the crushing chamber leads to material blockage; Broken or worn accessories; Poor lubrication causes the spindle to be tightly wrapped by a bushing
Solution: Tighten the bolts and pour them; Control the type of feed and prohibit non crushed materials from entering; Strictly control the feeding amount; Shutdown inspection of accessories; Replace damaged parts, inspect oil pumps and pipelines.
07 crusher vibrates strongly, and the cone part of the crusher rotates very high.
Cause: Lack of oil or dust in the oil between the main shaft and lining sleeve; Insufficient clearance of the conical liner; Wear or manufacturing reasons of bowl shaped bearing tiles, contact surface depth reaching inner circle, and sinking of conical body.
Solution: Repair or replace bushings, spindles, etc., and identify the cause of oil shortage to eliminate it; Adjust the clearance between the bushings; Re scratch and meet the requirements.
08 moving cone suddenly revs up.
Cause: sinking of the moving cone or damage to the spherical thrust bearing; The movement of the conical liner causes insufficient clearance between it and the spindle.
Solution: Adjust the gap.
09The transmission shaft rotates unevenly, producing a strong knocking sound. After that, the pulley rotates and the cone does not move.
Cause: Severe gear wear or damage; Damaged connection key; The spindle is broken.
Solution: Stop the machine and replace the gears, and ensure that the meshing clearance meets the requirements; Replace the connection key; Replace the spindle and strengthen the iron removal work.
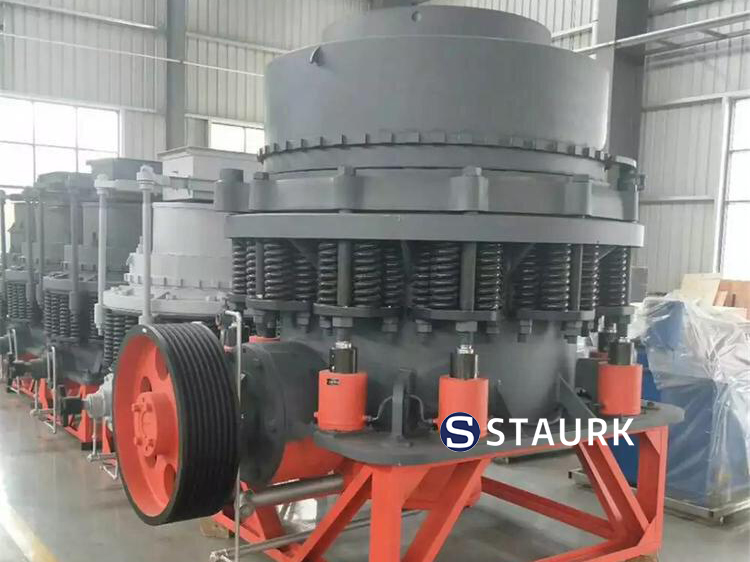
10. An audible splitting sound is produced during crushing or idling.
Cause: Loose lining board; Impact caused by non circular lining plates of moving or fixed cones.
Solution: Stop the machine and check the tightening of the screws and the detachment of the zinc layer.
11 tapping sounds, the coupling rotates and the crusher does not move.
Cause: Key breakage of the transmission coupling or gear; The spindle is broken.
Solution: Disassemble and replace with a new one; Disassemble and inspect for replacement.
12 drive shaft rotates unevenly, producing a strong knocking sound.
Cause: Improper installation of bevel gears, poor meshing, excessive clearance, excessive axial clearance of the transmission shaft, or gear damage.
Solution: Correct the meshing clearance or replace the gear.
13. There was a loud impact sound, and the support ring jumped up and then returned to normal operation.
Cause: Non crushing materials fall into the crushing chamber, which can easily cause the spindle to break.
Solution: Strengthen iron lifting or install iron removers.
14. The particle size of the ore discharge increases.
Cause: The lining plate is severely worn.
Solution: Adjust the discharge port and reduce the size of the discharge port; Replace the lining plate.
The above are some common problems encountered in the production of cone breakage. The causes and solutions have been attached. If there are any shortcomings, please leave a message for correction!