Ilmenite including Titanium Ore and ilmenite sand, usually in sand mining,it also contains Titanium ore, hematite, monazite, yttrium phosphate, zircon, cassiterite, etc,so processing plant Relatively complex.
1.Ilmenite sand processing plant
The main deposit types of ilmenite sand ore are seashore sand ore, followed by residual slope sand ore and alluvial sand ore.
Sand ore is the main source of mineral products such as ilmenite, rutile, zircon and monazite in the world.
The sand ore concentrator is divided into two parts: roughing and concentrating.
A Roughing
The ore entering the roughing plant is deslagging, screening, grading, desludging and concentrating, and then enters the roughing process for selection. The purpose of roughing is to provide rough concentrate for the concentrating plant. According to the mineral density, the selected ore is re-selected by discarding a large amount of low gangue to obtain a heavy mineral mixed concentrate with a heavy mineral content of about 90%.
Roughing generally uses equipment with strong processing capacity, high efficiency, light weight, and convenient for mobile concentrators. Most of them use equipment such as cone concentrators and spiral concentrators, and a few use shaking tables.
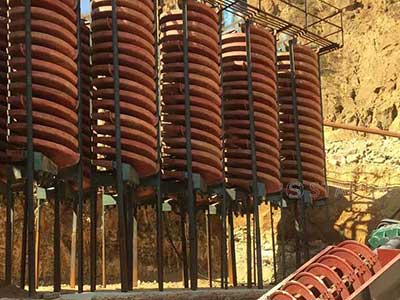
spiral concentrators
B Concentrating
Concentrators are generally built in fixed types. Concentration operations are divided into wet concentrating and dry concentrating, with dry concentrating being the main type.
The front end of the selection process often uses wet operations to further discard low-density gangue minerals. In the selection process, there is often a phenomenon of alternating between wet and dry.
Dry concentrating is to sort according to the differences in the magnetic properties, conductivity, density and other properties of minerals.
Magnetism and conductivity of common minerals table
2. Titanium ore processing line
The primary minerals being developed in industry are all composite deposits containing iron and titanium. The ore selection process is divided into two parts: iron selection and titanium selection.
A Iron selection
The main purpose of using composite ores containing iron and titanium in industry is to obtain iron concentrate and vanadium iron concentrate.
First, the selected ore is crushed (by Jaw crusher , cone crusher , ball mill , roller crusher etc)and ground to dissociate most of the iron minerals and other mineral monomers, and then a wet weak magnetic field magnetic separator is used to select iron concentrate or iron vanadium concentrate. The magnetic tailings are the raw materials for comprehensive recovery of titanium.
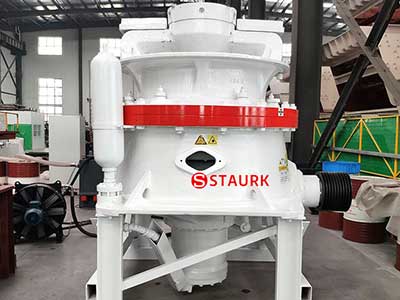
Cone crusher
In some ores, iron and titanium minerals are densely embedded, and it is difficult to obtain a separate concentrate using a single beneficiation method. Therefore, after discarding the tailings through gravity separation or other methods, the obtained iron-titanium mixed concentrate is directly roasted and smelted to produce high-purity pig iron and head slag.
B Titanium selection
The tailings from iron selection are used for titanium selection. Titanium selection methods include gravity separation, magnetic separation, electrostatic separation and flotation. There are several industrial titanium selection process flows:
(1) Gravity separation-electrostatic separation process. Gravity separation is used to discard low-density gangue or waste rock minerals, and the obtained coarse concentrate is then electrostatically separated to obtain ilmenite concentrate. For sulfur-containing ores, flotation is required to remove sulfide minerals before electrostatic separation.
(2) Gravity separation-magnetic separation-flotation process. The materials to be selected are first classified, and the coarse particles are removed by gravity separation and magnetic separation, and the fine particles are removed by flotation to obtain titanium concentrate.
(3) Coarse particle gravity separation-electrostatic separation and fine particle magnetic separation-flotation process. The characteristic of this process is that the selected materials are divided into coarse and fine parts. The coarse particles are processed by gravity roughing and electrostatic separation; the fine particles are roughly separated by magnetic separation, and then flotation is used to obtain fine titanium concentrate.
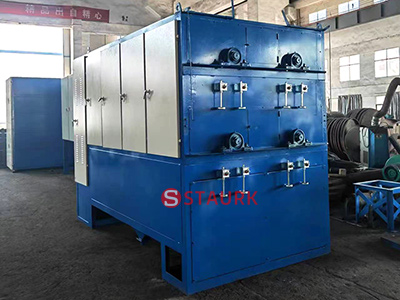
High tension separators
(4) Single flotation or magnetic separation-flotation process. For ilmenite ore with fine particle size, after grinding and iron separation, titanium concentrate is directly obtained by flotation, or a wet high-intensity magnetic separator is used as a roughing device, and then the magnetic part of the magnetic separation is recovered by flotation. The process flow of single flotation or magnetic separation-flotation is relatively simple and easy to operate and manage, but the use of flotation reagents will increase the cost of mineral processing.