Which need in tin mining processing plant dressing beneficiation machine flow chart
2025-01-17
Staurk
Which machine needed in a tin mining processing plant ?
The ore enters the jig machine gravity separate. The jig can achieve enrichment and separation based on the density difference of the ore, improving the grade and yield of tin ore.
The process flow of tin ore beneficiation mainly includes two : Gravity and flotation.
Comparied with flotation, Gravity is most pouplar .And usually flotation if needed, will arrange behind of gravity.
Gravity plant machine steps
Comparied with flotation, Gravity is most pouplar .And usually flotation if needed, will arrange behind of gravity.
Gravity plant machine steps
1.Pre treatment of washing and screening:
Using a washing and screening integrated circular drum washing machine to preliminarily wash and screen the ore, remove surface soil and impurities, and improve the grade of tin ore
Using a washing and screening integrated circular drum washing machine to preliminarily wash and screen the ore, remove surface soil and impurities, and improve the grade of tin ore
2.Crusher & grinding
Tin ore first needs to go through process steps such as collection, crushing(eg. jaw crusher , hammer crusher ), and grinding(eg. ball mill , tyre ball mill ) to ensure that the particle size of the ore is appropriate for subsequent beneficiation operations.
Usually by crusher, make tin size below 25mm, then feed into ball mill, to grind it into suitable size(usually 100 - 180 mesh)
3.Gravity separation:
Tin ore first needs to go through process steps such as collection, crushing(eg. jaw crusher , hammer crusher ), and grinding(eg. ball mill , tyre ball mill ) to ensure that the particle size of the ore is appropriate for subsequent beneficiation operations.
Usually by crusher, make tin size below 25mm, then feed into ball mill, to grind it into suitable size(usually 100 - 180 mesh)
3.Gravity separation:
The ore enters the jig machine gravity separate. The jig can achieve enrichment and separation based on the density difference of the ore, improving the grade and yield of tin ore.
Through the force of shaking table, the ore is layered in the water flow, achieving enrichment and separation, and further improving the grade of tin ore.
Tailings treatment:The tailings are treated to reduce resource waste and achieve green production, the water can be re-used after thickener.
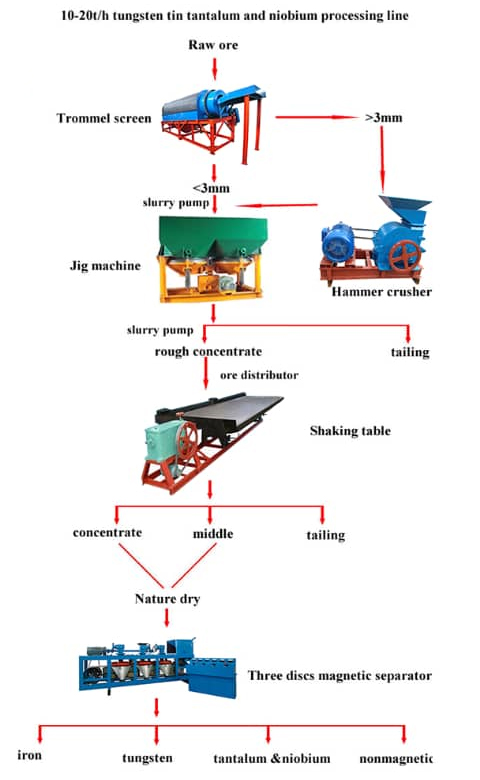
Flotation plant machine steps
Rough selection stage: After grinding with a rod mill, the ore is pre selected and tailings are discarded using a jigs to maximize the ore grade while ensuring the recovery rate of tin minerals
Selection stage: After grinding, the ore enters the shaker for selection, and the grade of tin ore is further improved through equipment such as shaker, spiral chute, and jigs
Flotation reselection combined process: For fine-grained disseminated cassiterite sulfide ores, the method of flotation desulfurization followed by reselection for tin selection is adopted, and this combined process has a better treatment effect
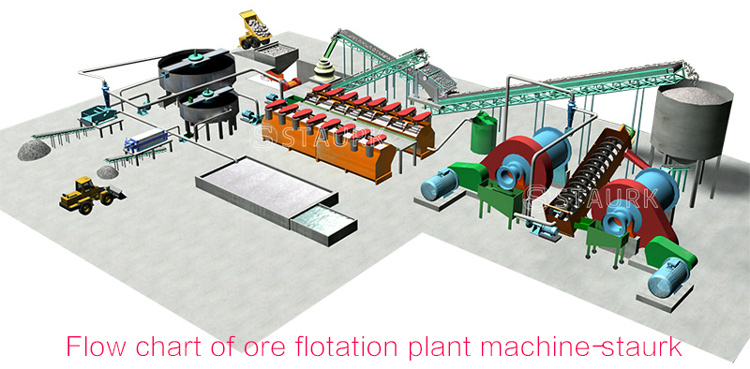
Mineral processing methods for different types of tin ores
Coarse grained embedded tin ore: Usually, the concentrate or coarse concentrate of tin is directly selected by gravity selection, and the beneficiation process for this type of tin ore is the simplest
Fine grained embedded tin ore: requires desulfurization first, followed by re-election, with high equipment investment and production costs
Uneven distribution of tin ore with uneven thickness: It is necessary to adopt a multi-stage grinding and multi-stage sorting process according to the actual situation